A Comprehensive Guide to BGA Substrate Materials and Their Types
BGA (Ball Grid Array) Substrate Materials are essential components in the packaging of modern electronic devices. They serve as the foundation for mounting integrated circuits (ICs) onto a PCB (Printed Circuit Board). The BGA Substrate Materials provide the necessary support for the solder balls that connect the chip to the board, ensuring reliable electrical and mechanical performance. These materials must meet strict requirements for thermal conductivity, electrical insulation, and mechanical strength to withstand the demanding conditions in high-performance electronics.
The significance of BGA Substrate Materials in modern electronic packaging cannot be overstated. As electronic devices continue to become smaller and more powerful, the need for efficient heat dissipation and robust signal transmission increases. BGA Substrate Materials are designed to meet these needs, offering superior performance in compact, high-density configurations. Their versatility makes them ideal for applications ranging from consumer electronics to automotive systems, where both performance and reliability are crucial.
Types of BGA Substrate Materials: A Comprehensive Overview
BGA Substrate Materials come in various types, each offering unique characteristics to meet the diverse needs of electronic packaging. The choice of material can significantly impact the performance, reliability, and cost of the final product. Below, we explore the main types of BGA Substrate Materials:
Organic Materials
Organic materials are the most commonly used in BGA substrates, offering a balance of cost-effectiveness and performance. The most popular organic materials include:
- FR4: A widely used, affordable option, FR4 is a fiberglass-reinforced epoxy resin that provides good electrical insulation and mechanical strength. However, its thermal performance is lower than other materials, which may limit its use in high-power applications.
- BT Resin: A higher-performance organic material, BT resin (Bismaleimide-Triazine) offers better thermal stability and lower coefficient of thermal expansion (CTE) than FR4. It is often used in high-density interconnect (HDI) designs and applications requiring better thermal management.
- Polyimide: Known for its excellent thermal resistance, polyimide is used in applications where extreme temperature fluctuations are expected. It provides good flexibility and electrical properties, making it suitable for flexible substrates and thin-film packaging.
Ceramic Materials
Ceramic BGA substrates are known for their superior thermal conductivity, mechanical strength, and stability under high temperatures. Common ceramic materials include:
- Alumina: Alumina (Al2O3) is a popular ceramic material used for BGA substrates due to its high thermal conductivity and electrical insulation properties. It is ideal for power electronics and other applications where heat dissipation is critical.
- Aluminum Nitride: Aluminum nitride (AlN) offers even better thermal conductivity than alumina, making it highly suitable for high-power devices and systems requiring efficient heat management. It is more expensive than alumina but provides superior performance in high-demand environments.
Flexible and Laminated Substrates
Flexible substrates are gaining popularity in BGA packaging, especially for wearable electronics, flexible displays, and mobile devices. These substrates allow for more compact designs and can be bent or folded without compromising functionality. Key materials include:
- Flexible Polyimide: Often used in flexible circuits, polyimide substrates allow for bending without sacrificing performance. They are ideal for devices that require both flexibility and high electrical reliability.
- Laminated Substrates: These substrates are constructed by layering different materials to achieve desired properties such as higher mechanical strength or better heat resistance. Laminated BGA substrates are often used in complex, high-performance applications that require enhanced structural integrity.
How Different BGA Substrate Materials Impact Performance
The choice of BGA Substrate Material plays a crucial role in the performance of the electronic device. Organic materials like FR4 are cost-effective and suitable for many standard applications but may not offer the thermal stability required for high-performance, heat-sensitive devices. Ceramic materials, while more expensive, are ideal for applications where heat dissipation and mechanical stability are critical, such as power electronics. Flexible and laminated substrates provide design flexibility and are crucial for emerging technologies like wearables or flexible displays.
Ultimately, the selection of BGA Substrate Materials depends on the specific requirements of the application, such as thermal performance, mechanical strength, electrical insulation, and cost considerations. As technology advances, new materials and manufacturing techniques continue to evolve, allowing for more efficient, high-performance BGA packaging solutions.
BGA Substrate Materials in Flip-Chip BGA Packaging
Flip-Chip Ball Grid Array (FC-BGA) packaging represents an advanced technology that has become widely used in high-performance electronic devices. Unlike traditional BGA packaging, Flip-Chip BGA offers significant advantages in terms of thermal management, electrical performance, and miniaturization. The choice of BGA Substrate Materials plays a crucial role in ensuring the performance and reliability of FC-BGA packages.
What Makes Flip-Chip BGA Different from Other Packaging Technologies?
Flip-Chip BGA differs from conventional BGA packaging in its structure and assembly process. In a traditional BGA, the chip is mounted with its bond pads facing up, and the connection to the PCB is made through solder balls placed beneath the chip. However, in Flip-Chip BGA packaging, the chip is flipped over so that its active surface faces downward toward the PCB, with solder bumps directly connecting the chip to the substrate.
This flip-over method allows for the following benefits:
-
Reduced Package Height: Because the chip is flipped and the interconnection occurs directly between the chip and the PCB, Flip-Chip BGA packages can be significantly thinner than traditional packages. This is especially beneficial in devices where space is limited, such as smartphones, laptops, and wearable electronics.
-
Improved Heat Dissipation: Direct solder bumping between the chip and substrate provides a better thermal path, improving heat dissipation. This makes FC-BGA ideal for high-performance applications that generate significant heat, such as processors and GPUs.
-
Enhanced Electrical Performance: The flip-chip process reduces the length of the interconnections between the chip and the substrate, leading to lower inductance and resistance. This results in improved electrical performance and higher signal integrity, especially at high speeds.
Advantages of Using Specific BGA Substrate Materials for Flip-Chip BGA (FC-BGA) Packages
The selection of BGA Substrate Materials for FC-BGA packaging is critical for maximizing the benefits of this advanced packaging technique. Several specific materials are preferred due to their ability to meet the demanding requirements of Flip-Chip BGA.
-
Organic Materials (e.g., BT Resin and Polyimide)
- Thermal Management: BT resin, in particular, is favored for FC-BGA packages due to its excellent thermal stability and low coefficient of thermal expansion (CTE). This is vital for maintaining reliability under temperature fluctuations, as mismatched CTEs between the substrate and the chip can lead to mechanical stress and failure.
- Cost-Effectiveness: Organic materials like BT resin and polyimide offer a cost-effective alternative to ceramics, making them ideal for mass-produced consumer electronics while still providing good performance in thermal management and signal integrity.
-
Ceramic Materials (e.g., Alumina, Aluminum Nitride)
- Superior Thermal Conductivity: Ceramic materials such as aluminum nitride (AlN) are used in FC-BGA packages where heat dissipation is a top priority. These materials offer much higher thermal conductivity compared to organic materials, making them ideal for high-power applications like processors and power amplifiers. The improved thermal management helps to prevent overheating and ensures the long-term reliability of the device.
- Mechanical Stability: Ceramic BGA substrates also provide excellent mechanical strength, ensuring that the package remains intact even in high-stress environments. This is particularly important for applications like automotive or industrial electronics, where vibrations and external stresses can be significant.
-
Laminated Substrates
- Enhanced Mechanical Strength and Electrical Performance: Laminated substrates, which are made by layering different materials, offer a balance between the electrical performance of ceramics and the cost-effectiveness of organic materials. These substrates can be engineered to provide the necessary properties for specific Flip-Chip BGA applications, such as improved mechanical strength or better electrical performance in high-frequency applications.
- Customization: Laminated substrates are also highly customizable, allowing manufacturers to tailor the substrate to the specific needs of the device. This makes them ideal for complex, high-performance FC-BGA packages used in advanced computing, telecommunications, and aerospace applications.
-
Flexible Substrates
- Bendable and Durable: For applications requiring flexible and lightweight packaging, such as wearable devices or flexible electronics, polyimide-based flexible substrates are used. These materials allow for the creation of FC-BGA packages that maintain electrical and mechanical integrity even when bent or deformed. The use of flexible BGA Substrate Materials enables the production of devices that can be folded, rolled, or curved without compromising functionality.
The choice of BGA Substrate Materials is integral to the performance and reliability of Flip-Chip BGA (FC-BGA) packages. By using specific materials like BT resin, aluminum nitride, and flexible polyimide, manufacturers can optimize thermal performance, signal integrity, and mechanical strength, making FC-BGA an ideal solution for high-performance electronics. The flexibility in material selection allows for the customization of FC-BGA packages, enabling their use in a wide range of industries, from consumer electronics to automotive and aerospace applications.
Get a Quotation For BGA Substrate Materials Now
Understanding the Role of BGA Substrate Materials in BGA Underfill
BGA Underfill is a critical material used in Ball Grid Array (BGA) packaging to enhance the mechanical and thermal reliability of the solder joints between the chip and the substrate. It plays a key role in improving the overall durability and longevity of BGA assemblies, especially in high-performance applications where thermal cycling, mechanical stress, and vibration are concerns.
What is BGA Underfill, and How Does It Relate to BGA Substrate Materials?
BGA Underfill is a polymeric material that is applied between the BGA chip and the BGA substrate after the soldering process. It is typically a type of epoxy resin that flows into the gap between the chip and the substrate, filling the space around the solder balls. The underfill material then cures, hardening to provide additional structural support to the solder joints and ensuring better heat dissipation.
The relationship between BGA Substrate Materials and Underfill is crucial because the selection of substrate material influences the performance of the underfill. The underfill material must be compatible with the BGA Substrate Materials to ensure proper adhesion and effective thermal and mechanical properties. For instance, different substrates have varying coefficients of thermal expansion (CTE), which can cause stress at the solder joints due to temperature fluctuations. A good underfill material will help mitigate these stresses by absorbing the strain and ensuring long-term reliability of the solder joints.
Key Materials Used for BGA Underfill and Their Compatibility with BGA Substrate Materials
-
Epoxy-Based Underfills
- Characteristics: Epoxy-based underfills are the most commonly used due to their excellent adhesion, low viscosity, and good flow characteristics. These underfills are particularly effective in protecting the solder joints from mechanical stress and thermal cycling. They are also highly durable and provide good moisture resistance, which is essential for the longevity of BGA packages.
- Compatibility with BGA Substrate Materials: Epoxy underfills are generally compatible with a wide range of BGA Substrate Materials, including organic materials like FR4 and BT resin. However, for high-performance applications involving ceramic substrates, such as aluminum nitride (AlN), special formulations of epoxy underfill with enhanced thermal conductivity are required to match the thermal properties of the ceramic substrate.
-
Silicone-Based Underfills
- Characteristics: Silicone-based underfills are known for their flexibility and superior thermal stability. These underfills can withstand extreme temperature variations and are highly resistant to thermal shock. Silicone underfills also exhibit low shrinkage during curing, which helps to minimize mechanical stress on the solder joints.
- Compatibility with BGA Substrate Materials: Silicone underfills are particularly suitable for flexible and laminated substrates, such as polyimide or other flexible organic materials. They are ideal for applications that experience significant thermal expansion or physical movement, such as flexible electronics, automotive, or wearable devices.
-
Polyimide-Based Underfills
- Characteristics: Polyimide-based underfills offer excellent high-temperature stability and are often used in environments where components will be exposed to extreme conditions. These underfills provide exceptional resistance to thermal cycling and are typically used in high-reliability applications, such as aerospace or automotive electronics.
- Compatibility with BGA Substrate Materials: Polyimide underfills are particularly compatible with polyimide-based substrates, as both materials share similar thermal properties and coefficients of expansion. They are also used with ceramic substrates, as they can withstand the high-temperature environments that these substrates are designed for.
-
No-Flow Underfills
- Characteristics: No-flow underfills are designed to be applied before the soldering process and cure without requiring additional heat. These materials flow into the gaps between the chip and substrate during reflow soldering and form a strong bond with both the chip and the substrate.
- Compatibility with BGA Substrate Materials: No-flow underfills are compatible with a variety of BGA Substrate Materials, including both organic and ceramic substrates. However, the key to successful application lies in the precise control of temperature and time during the soldering process, ensuring that the underfill flows properly into the gaps and adheres strongly to both the chip and the substrate.
-
Conductive Underfills
- Characteristics: Conductive underfills are specialized materials that contain conductive fillers, such as silver or copper, which allow for electrical conductivity between the chip and the substrate. These underfills are used in applications where enhanced electrical performance is required, such as in high-frequency circuits or sensitive components.
- Compatibility with BGA Substrate Materials: Conductive underfills are more commonly used with ceramic substrates, where high thermal conductivity is needed, and with specialized organic substrates designed to support high-frequency signals. However, the conductive fillers must be carefully chosen to ensure they do not cause short circuits or other electrical issues in the package.
BGA Underfill plays an essential role in ensuring the reliability and performance of Ball Grid Array packages. The compatibility of underfill materials with BGA Substrate Materials is critical for achieving optimal mechanical support, thermal management, and electrical performance. By selecting the right underfill material—whether epoxy-based, silicone-based, polyimide-based, no-flow, or conductive—manufacturers can enhance the durability of BGA packages, protect against mechanical stresses, and ensure high performance under a range of environmental conditions. This synergy between BGA Substrate Materials and underfill materials is what makes BGA packaging a reliable solution for modern electronic devices.
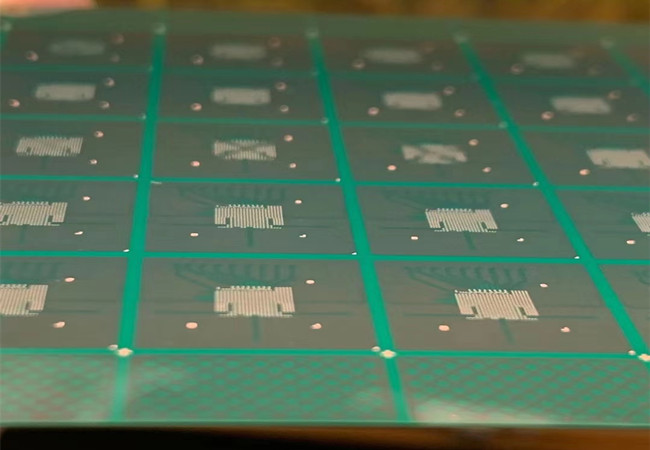
BGA Substrate Materials and Their Impact on Price
The choice of BGA Substrate Materials plays a significant role in determining the overall cost of BGA packages. Different materials vary in terms of performance characteristics, manufacturing complexity, and raw material costs. These factors, combined with specific application requirements, have a direct impact on the final price of the packaged components. Understanding how BGA Substrate Materials influence pricing is crucial for manufacturers, as it allows them to make informed decisions based on both performance needs and budget considerations.
How the Choice of BGA Substrate Materials Affects Overall Pricing
The selection of BGA Substrate Materials impacts both the initial production costs and long-term expenses associated with the device. The material chosen affects several factors:
-
Material Costs: Different BGA Substrate Materials come with varying price tags based on their intrinsic properties. For instance:
- Organic Materials such as FR4 (fiberglass-reinforced epoxy resin) are relatively inexpensive compared to other options, making them a popular choice for mass-market applications where cost control is essential. These substrates offer a balance of performance and cost, making them ideal for consumer electronics and other high-volume products.
- Ceramic Materials like aluminum nitride (AlN) and alumina are more expensive due to their superior thermal conductivity and mechanical strength. Ceramic substrates are typically used in high-performance applications such as power electronics, where the performance demands justify the higher cost.
- Flexible and Laminated Substrates are also costlier than organic materials. Flexible substrates made from polyimide or other high-performance polymers are more expensive due to their ability to withstand harsh conditions and their applications in niche markets like wearable devices or automotive electronics.
-
Impact on Manufacturing Processes: The complexity of manufacturing processes required for different BGA Substrate Materials also influences the overall price.
- Organic Substrates like FR4 or BT resin are relatively straightforward to process, leading to lower production costs. Their widespread availability and established manufacturing techniques contribute to their lower pricing.
- Ceramic Substrates, on the other hand, require more specialized manufacturing processes, such as high-temperature sintering, precision cutting, and bonding. These additional processing steps increase both the labor and energy costs associated with production, resulting in higher substrate costs.
- Flexible and Laminated Substrates may require additional steps for lamination, etching, and customization, which can further drive up the production costs.
-
Yield and Defect Rates: Substrates with more complex manufacturing processes often result in higher defect rates, which increase the cost per unit. Materials like ceramics and certain flexible substrates require more precise handling and processing to maintain high yield rates. A higher defect rate means more materials are wasted during production, leading to an overall increase in cost for high-quality products.
Factors Influencing the Cost of BGA Substrate Materials
Several factors influence the pricing of BGA Substrate Materials beyond the base material itself. These factors include:
-
Material Type:
- The raw material used directly influences the cost. For example, high-performance materials like aluminum nitride and polyimide are costlier than more common materials like FR4 due to the extraction and refinement processes required for their production. The availability of raw materials also impacts pricing—materials that are abundant and easy to source tend to be cheaper, while rarer or specialty materials can drive up the price.
-
Manufacturing Processes:
- Different BGA Substrate Materials require different production methods, which impact both the direct and indirect costs. Organic substrates are typically mass-produced using well-established processes like lamination and etching, which reduce production costs. Conversely, ceramic substrates demand higher precision in their manufacture due to the need for high-temperature sintering, which increases the overall production cost. Similarly, flexible substrates may involve additional processing steps such as lamination and curing, which further raise costs.
-
Supply Chain and Availability:
- The cost of BGA Substrate Materials is also influenced by global supply chain factors. For example, ceramic materials are often sourced from specific regions where they are mined or produced in limited quantities. Disruptions in the supply chain—whether due to geopolitical tensions, natural disasters, or raw material shortages—can cause fluctuations in pricing.
- Similarly, flexible and laminated substrates may be sourced from specialized manufacturers who offer tailored solutions, further increasing the cost due to the lower volume and higher customization involved.
-
Market Demand:
- High demand for specific types of substrates, such as ceramic substrates used in high-power applications, can drive up prices. Conversely, materials like FR4 that are used in mass-market consumer electronics are often less expensive because they are produced in large quantities to meet high-volume needs.
- The trend toward miniaturization and the rise of applications like flexible electronics and wearable devices have led to a greater demand for flexible substrates, which has contributed to higher prices for these materials.
-
Technological Advancements:
- As technology evolves, new materials and manufacturing techniques emerge, influencing the cost of BGA Substrate Materials. Advanced organic materials or new types of ceramics with improved performance characteristics may come at a premium due to research and development costs, as well as the need for specialized equipment and processes to manufacture them.
- Additionally, environmental regulations and sustainability concerns may also drive up the cost of certain materials. For example, the use of certain chemicals or processes may become restricted, requiring manufacturers to adopt more expensive, environmentally friendly alternatives.
The choice of BGA Substrate Materials directly affects the overall price of the BGA package. While organic materials like FR4 are cost-effective and suitable for high-volume production, more advanced materials such as ceramics and flexible substrates drive up the price due to their superior performance characteristics and more complex manufacturing processes. Factors such as material type, manufacturing processes, and global supply chain dynamics all play a role in determining the final cost of the substrate. Manufacturers must carefully balance performance requirements with cost constraints to select the most appropriate material for their specific application, ensuring both high quality and cost-effectiveness.
Get a Quotation For BGA Substrate Materials Now
Leading BGA Substrate Materials Suppliers in the Market
The global BGA Substrate Materials market is highly competitive, with several key players leading the supply of materials for Ball Grid Array (BGA) packaging. These suppliers are known for providing high-quality substrates that meet the demanding requirements of modern electronics, including high thermal performance, electrical integrity, and mechanical reliability. In this section, we will explore some of the leading suppliers, such as Shinko, Kyocera, and Venture MFG, who play a significant role in shaping the BGA Substrate Materials market.
Overview of Top Global Suppliers of BGA Substrate Materials
-
Shinko Electric Industries Co., Ltd. Shinko is one of the most well-known names in the BGA Substrate Materials industry, particularly when it comes to ceramic substrates. With decades of experience, Shinko has established itself as a leading supplier for both high-performance and consumer electronics. The company’s ceramic BGA substrates are widely used in applications that demand superior thermal conductivity, mechanical strength, and reliability.
- Products and Specialization: Shinko offers a variety of substrates, including PBGA (Plastic Ball Grid Array), FCBGA (Flip Chip Ball Grid Array), and CSP (Chip-on-Board Substrate) solutions. The company is also known for its high-density interconnect (HDI) substrates, which are used in cutting-edge electronics.
- Technology: Shinko is a pioneer in ceramic-based substrates, offering alumina and aluminum nitride (AlN) substrates that are essential for applications like power electronics, automotive, and industrial applications. These materials are ideal for environments where high power density and heat dissipation are critical.
- Global Presence: Shinko’s manufacturing plants are located in Japan, and the company serves a global customer base, including major semiconductor manufacturers.
-
Kyocera Corporation Kyocera, another industry giant, is renowned for its advanced materials and packaging solutions. The company supplies a wide range of BGA Substrate Materials for both consumer electronics and more specialized applications.
- Products and Specialization: Kyocera’s FCBGA and LGA (Land Grid Array) substrates are highly regarded for their superior thermal performance and reliability in critical applications like mobile processors, memory modules, and automotive systems. Kyocera also manufactures substrates that combine organic and ceramic materials, offering a hybrid solution that balances the cost-efficiency of organic materials with the high performance of ceramics.
- Technology: Kyocera excels in organic BGA substrates such as BT resin-based substrates, which offer excellent electrical and mechanical properties. In addition to organic substrates, Kyocera specializes in the production of ceramic substrates with high reliability and durability under harsh conditions.
- Global Reach: Kyocera’s expertise extends beyond the semiconductor industry. With a global presence, they supply BGA substrates to various sectors, including consumer electronics, automotive, telecommunications, and industrial applications.
-
Venture Manufacturing Venture Manufacturing is another significant player in the BGA substrate materials market. Based in the United States, Venture specializes in the design and manufacturing of BGA Substrate Materials that cater to both flip-chip and traditional ball-grid array packaging solutions.
- Products and Specialization: Venture offers a diverse range of PCB and IC substrate materials, including FR4-based substrates, BT resin, and specialized ceramic substrates. The company is particularly noted for its capabilities in customizing substrates to meet specific customer requirements for electrical performance, thermal management, and mechanical strength.
- Technology: Venture is at the forefront of providing cost-effective solutions that cater to high-volume production. They also focus on high-frequency applications, making them a preferred supplier for telecommunications and aerospace industries.
- Global Operations: While primarily based in the U.S., Venture Manufacturing has a strong supply chain presence in Asia and serves customers worldwide, making it a go-to choice for companies looking for cost-effective yet high-quality BGA substrate materials.
Other Notable Suppliers
-
Jiangsu Changjiang Electronics Technology Co., Ltd. (JCET) JCET is one of the largest semiconductor packaging and testing companies in China. They are a major supplier of BGA Substrate Materials and offer a wide variety of packaging solutions, including FCBGA, CSP, and SiP (System-in-Package) solutions. JCET’s expertise lies in providing high-density substrates that support high-speed, high-frequency, and power-sensitive applications.
-
Unimicron Technology Corporation Unimicron is a Taiwanese company that specializes in PCB and substrate manufacturing. It is one of the largest suppliers of organic substrates, with an emphasis on high-density interconnects and advanced packaging technologies. Unimicron’s products are used extensively in consumer electronics, automotive, and communication systems.
-
Shenzhen BGT Electronics Co., Ltd. Based in China, BGT Electronics specializes in the manufacturing of flexible substrates and high-performance BGA substrates for applications in the wearable and automotive electronics sectors. Their expertise in polyimide-based substrates makes them an ideal supplier for companies looking to implement flexible electronics solutions.
The leading suppliers of BGA Substrate Materials, such as Shinko, Kyocera, and Venture Manufacturing, offer a broad range of products that meet the varied needs of industries like telecommunications, automotive, consumer electronics, and power electronics. These companies have established themselves as key players through their advanced technologies, extensive product portfolios, and global manufacturing capabilities. The market for BGA substrates continues to grow, driven by advancements in packaging technologies and the increasing demand for high-performance, reliable electronic devices. As companies like Shinko, Kyocera, and Venture Manufacturing continue to innovate, they play a crucial role in shaping the future of BGA Substrate Materials and semiconductor packaging technologies worldwide.
Get a Quotation For BGA Substrate Materials Now
What Are BGA Chips Made Of and How BGA Substrate Materials Fit In?
BGA (Ball Grid Array) chips are a type of semiconductor package used to provide electrical connections between a microchip (such as a processor or memory device) and a printed circuit board (PCB). The design of BGA chips is distinct because the connections are made through solder balls arranged in a grid pattern on the bottom of the package. These chips are critical components in electronic systems, offering high performance, compact size, and reliability. To understand how BGA Substrate Materials fit into the assembly and performance of these chips, we must first break down the materials that make up a BGA chip and examine how the substrate contributes to its overall functionality.
Breakdown of BGA Chip Materials (Silicon, Solder Balls) and Their Integration with BGA Substrate Materials
-
Silicon Chip (Semiconductor Die)
- Material Composition: The core of any BGA chip is the silicon die, which is the semiconductor material that performs the computational tasks. Silicon is chosen for its excellent electrical conductivity, ease of manufacturing, and ability to be doped with impurities to control its electrical properties.
- Integration with Substrate: Once the silicon die is fabricated, it is attached to a BGA substrate using a process called die attach. The substrate serves as the base that houses the die and provides the necessary interconnects between the die and the external PCB. This is where BGA Substrate Materials come into play, providing the platform for mounting the silicon die and ensuring proper electrical and mechanical connections.
-
Solder Balls (Interconnects)
- Material Composition: The solder balls used in BGA packaging are typically made from an alloy of tin (Sn) and lead (Pb), though lead-free solder alloys, such as tin-silver-copper (SAC), are increasingly common due to environmental regulations. These solder balls are placed in the grid pattern on the bottom of the BGA package and are used to create the electrical connections to the PCB.
- Integration with Substrate: The solder balls form a direct electrical connection between the BGA chip and the PCB by melting during the soldering process and forming joints with the copper pads on the PCB. The BGA Substrate Materials provide the required pads and traces that link the solder balls to the chip’s circuitry and allow for the signal and power to be transmitted to the PCB.
-
Die Attach Materials
- Material Composition: Die attach materials, typically epoxy resins, are used to bond the silicon die to the BGA substrate. These materials must have good thermal conductivity and adhesion properties to ensure that the heat generated by the chip is dissipated efficiently and the chip remains securely in place.
- Integration with Substrate: The choice of die attach material is crucial for the overall performance of the BGA chip. The BGA Substrate Materials play a significant role in determining how well the die attach material adheres to both the die and the substrate, as well as how effectively heat is managed.
The Role of BGA Substrate Materials in the Assembly and Performance of BGA Chips
-
Electrical Performance
- The primary role of BGA Substrate Materials is to provide the necessary interconnects between the chip and the PCB. This includes the signal pathways, power distribution, and ground connections. The conductivity of the substrate materials, particularly in organic (FR4, BT resin) and ceramic (aluminum nitride, alumina) types, plays a significant role in the overall electrical performance of the chip. A high-quality substrate ensures that electrical signals travel with minimal resistance and interference, supporting high-frequency applications and reducing signal loss.
-
Thermal Management
- As the silicon die operates, it generates heat, which needs to be efficiently transferred away from the chip to prevent overheating. Thermal conductivity is one of the most critical aspects of BGA Substrate Materials. Ceramic materials, such as aluminum nitride (AlN), have a much higher thermal conductivity than organic materials like FR4. Substrates with higher thermal conductivity help dissipate heat more efficiently, ensuring that the chip operates within safe temperature ranges.
- In addition to the material itself, BGA Substrate Materials are designed with vias and thermal pads to channel heat away from the silicon die and into the PCB. This is especially important in high-power or high-performance applications, where heat management is crucial to prevent performance degradation and extend the lifespan of the chip.
-
Mechanical Support and Reliability
- The mechanical integrity of the BGA package is another key function of BGA Substrate Materials. The substrate must support the silicon die during the assembly process and throughout the operational life of the chip. The material properties, such as flexural strength and coefficient of thermal expansion (CTE), must match those of the silicon die to prevent mechanical stress that could lead to failure of the solder joints.
- When subjected to temperature cycles, the materials in the BGA substrate and the silicon die expand and contract. If the CTEs of the die and substrate are mismatched, it could lead to microcracking in the solder joints, compromising the long-term reliability of the package. Proper design and selection of BGA Substrate Materials ensure that this issue is minimized, improving the overall mechanical performance and longevity of the chip.
-
Cost and Manufacturing Efficiency
- The selection of BGA Substrate Materials also impacts the overall cost and manufacturing efficiency. Organic substrates like FR4 are widely used in lower-cost, high-volume applications due to their availability and ease of processing. However, for applications that demand higher performance (such as power electronics or automotive systems), ceramic substrates may be used, despite their higher cost and more complex manufacturing processes.
- Additionally, the complexity of the substrate design (e.g., the number of layers, the density of interconnects, and the size of the substrate) directly impacts the production time and cost. Manufacturers must balance the performance requirements of the chip with the cost constraints of the package to ensure both performance and profitability.
BGA chips are made of several materials, primarily silicon for the die and solder balls for interconnection. However, the BGA Substrate Materials play a crucial role in enabling the chip to function effectively by providing the necessary electrical, thermal, and mechanical support. The integration of these materials with the silicon die ensures efficient signal transmission, effective heat dissipation, and mechanical stability. The careful selection of BGA Substrate Materials directly influences the performance, reliability, and cost-effectiveness of the chip. Whether the application requires high thermal conductivity for power electronics or cost-effective solutions for consumer electronics, BGA Substrate Materials are essential in ensuring the chip performs as required under various operating conditions.
Get a Quotation For BGA Substrate Materials Now
Comparison: BGA Substrate Materials vs. PCB Materials
When it comes to modern electronics, BGA Substrate Materials and PCB (Printed Circuit Board) Materials are both essential components, yet they serve distinct roles and are made from different materials designed to meet specific performance and manufacturing requirements. Understanding the differences between BGA Substrate Materials and traditional PCB Materials is crucial for selecting the right materials for a given application. In this section, we will examine the key differences between these two types of materials and discuss performance considerations when choosing between them.
Key Differences in Materials Used for BGA Substrates vs. Traditional PCBs
-
Material Composition
- BGA Substrate Materials: BGA substrates are typically made from ceramic or organic materials. Ceramic substrates, such as alumina (Al2O3) and aluminum nitride (AlN), are used for their superior thermal conductivity and mechanical strength, making them ideal for high-performance applications. Organic substrates, such as BT resin and FR4, are also used, offering a balance of cost, ease of manufacturing, and performance. The choice of material depends on the thermal and electrical requirements of the package.
- PCB Materials: Traditional PCBs are typically made from laminated layers of epoxy resin reinforced with glass fiber (FR4) or polyimide. Other materials like CEM-1, CEM-3, and polyester are also used in specific applications, depending on the required flexibility, cost, and durability. While these materials are suitable for most electronic circuits, they generally have lower thermal conductivity and mechanical strength compared to ceramic substrates used in BGA packages.
-
Manufacturing Processes
- BGA Substrate Materials: The manufacturing process for BGA substrates is more complex compared to traditional PCBs. The substrates often require multi-layering for complex interconnects and the ability to handle high-frequency signals. The substrate must also accommodate the solder balls that connect the chip to the PCB. In addition, flip-chip configurations, where the chip is mounted face-down on the substrate, require precise alignment and special die-attach and underfill processes.
- PCB Materials: The manufacturing process for PCBs is typically simpler, involving fewer layers and less stringent requirements for high-frequency signals. While multi-layer PCBs can be produced, they are generally used in less complex designs compared to BGA substrates. PCBs are often manufactured using photolithography and etching techniques, and the interconnects are generally made using copper traces that run through the board.
-
Thermal Management
- BGA Substrate Materials: Thermal conductivity is a crucial factor in the design of BGA substrates. Since BGA chips can generate significant heat, especially in high-power applications, substrates made from ceramics (such as aluminum nitride) are often preferred due to their superior heat dissipation properties. Organic substrates, while less thermally efficient, are often used for less demanding applications.
- PCB Materials: While PCBs are also designed to manage heat, thermal conductivity is not as critical in traditional PCBs, except for high-power circuits. Materials like FR4 have relatively low thermal conductivity, which can lead to heat buildup in components if not properly managed. For this reason, heat sinks or additional thermal management solutions are often required in PCB designs, especially in power electronics.
-
Electrical Performance
- BGA Substrate Materials: BGA Substrates are designed with high electrical performance in mind. The interconnects on a BGA substrate are more advanced, using fine traces and vias that are capable of handling high-frequency signals and supporting high-density interconnects (HDI). The material selection for BGA substrates focuses on minimizing signal loss, maintaining signal integrity, and reducing electromagnetic interference (EMI).
- PCB Materials: Traditional PCBs are designed for lower-frequency circuits and generally do not support the high-density interconnects found in BGA packages. However, high-speed PCBs are used in some advanced electronics, such as communications and data transmission systems. These boards may use materials with enhanced electrical properties, such as teflon-based laminates or high-frequency materials, to reduce signal loss and support high-speed data.
Performance Considerations When Choosing Between BGA Substrate Materials and PCB Materials
-
Application Requirements
- The decision between BGA Substrate Materials and PCB Materials often depends on the specific requirements of the application. For example, BGA substrates are ideal for applications where high performance, thermal management, and density are crucial. This includes applications like mobile processors, memory modules, power modules, and automotive electronics. On the other hand, PCBs are sufficient for consumer electronics, low to moderate-speed circuits, and general-purpose systems that do not require the advanced performance capabilities of BGA substrates.
-
Cost Considerations
- BGA Substrate Materials tend to be more expensive than traditional PCB materials, mainly because of the complexity of the manufacturing process and the advanced properties required for BGA packaging. Ceramic substrates are particularly costly, though they offer superior performance in terms of thermal and electrical properties. For cost-sensitive applications, organic substrates such as FR4 and BT resin offer a middle ground between performance and price.
- PCBs are generally much less expensive to manufacture, particularly for simpler, single-sided designs. Their cost-effectiveness makes them the material of choice for most consumer electronics and low-cost applications.
-
Thermal Management Needs
- BGA Substrate Materials are essential when efficient thermal management is a top priority. The high-performance nature of ceramic-based BGA substrates allows them to handle higher power dissipation and thermal stress. In contrast, PCB materials may require additional thermal solutions such as heat sinks or cooling systems to manage heat in high-power applications.
-
Manufacturing Volume
- PCB Materials are typically used for high-volume production because they are easier and cheaper to produce. In contrast, BGA Substrate Materials are used for more specialized applications, particularly those requiring higher levels of integration and performance, which may limit the cost-effectiveness of high-volume manufacturing. However, high-volume applications requiring BGA packaging, such as smartphones and computers, often involve more intricate BGA substrates due to their superior performance characteristics.
The choice between BGA Substrate Materials and PCB Materials is primarily determined by the specific needs of the application, including performance requirements, thermal management, cost constraints, and manufacturing volume. While BGA Substrate Materials are designed for high-performance, high-frequency applications with advanced thermal and electrical demands, PCB Materials are typically used for simpler, lower-cost applications where the performance requirements are not as stringent. Each type of material has its strengths and weaknesses, and the decision between them should be made based on a careful analysis of the application’s needs. By understanding these key differences, engineers and designers can select the most suitable material to optimize the performance, reliability, and cost-effectiveness of their electronic devices.
Contact Us NOW
FAQs about bga substrate material
The substrate of a BGA (Ball Grid Array) is typically made of an insulating material, such as FR-4, BT resin, or polyimide.
BGA balls are usually made of solder, typically a lead-free alloy like tin-silver-copper (SnAgCu) or tin-bismuth (SnBi).
Inside a BGA, you’ll find several components, including the semiconductor die, the substrate, and the solder balls.
BGA type components encompass a range of integrated circuits (ICs) and semiconductor devices packaged using the BGA format, such as microprocessors, memory chips, and graphic processors.